總部位于加拿大安大略省喬治敦的 MHS 公司推出了第一款帶 8 個注塑腔的 M3 系列微注塑機。這個成功的注塑解決方案配備了倍福基于 PC 的控制技術和 EtherCAT 現場總線等產品。2020 年,MHS 公司決定將系統規模擴大到 32 腔,他們發現倍福平臺易于擴展,無需升級組件,并能夠繼續保持能夠延長塑料熔體使用壽命的創新工藝。
基于 PC 的控制助力優化微注塑機
無論注塑制品尺寸大小或采用的塑料材料類型如何,決定其品質的因素主要有三點:壓力、溫度和時間。Mold Hotrunner Solutions(MHS)2016 年推出的 M3 微注塑機對這些參數進行了優化。這種零廢棄交鑰匙注塑解決方案為醫療設備和電子制造商以及其他終端用戶提供了新的能力。M3-D08 系統配備公司自主研發的熱流道噴嘴和注射成型等技術,能夠高效、高精度地生產出重量輕至 1.3 mg 的直接澆口微型零件。
可靠的工藝是產品質量的保證
MHS 公司設計的 M3 系列旨在消除注射成型工藝中長期存在的缺陷。傳統上,注塑成型過程的第一步是將粒狀塑料從注塑機的料斗送入料筒中。螺桿推動粒狀塑料螺旋式向前輸送,料筒外的加熱器對其進行加熱熔化。通過合適的溫度控制程序,確保塑料在通過噴嘴注入模具之前達到所需的溫度和粘度。此外,M3 熱流道系統使用閥式澆口和內部熱切澆口將材料直接注入模具中。這樣就能夠生產出表面平整光滑的精密零件,并減少澆口殘留量,這些殘留物通常會聚集在澆口處,必須在零件后道成型工序中清除,以進行回收或丟棄。
若要打開和關閉模具,注塑機需要協調水平運動和垂直運動,在幾分之一秒內以 10 μm 精度調整重量為 500 磅(約 900 克)的模具位置。
這一過程對注塑機設計提出了挑戰,需要根據精確的壓力、溫度和時間規范提高注塑過程重復精度,以確保零件的高品質。
“倍福 2012 年就與 MHS 有過合作,當時他們需要性能更強大的自動化、通信和遠程訪問系統。”倍福加拿大區域銷售經理 Paul Pierre 說道。2016 年,MHS 要為完成 M3 系列的初始建造尋找新的控制解決方案,再次找到了倍福。一臺搭載四核 Intel® CoreTM i7 處理器的高性能 C6920 控制柜式工業 PC 被選為 M3 的控制平臺。一臺寬屏的 CP3921 控制面板用作 HMI 硬件。MHS 可以使用這臺 21.5 英寸的多點觸控顯示屏重新配置控制界面,以更好地適應微成型工藝,并可概覽所有工藝變量。
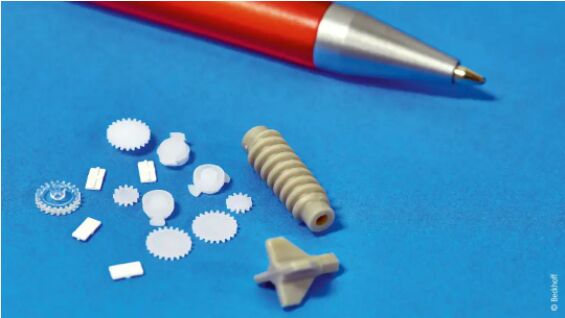
M3 微注塑機是生產醫療設備和電子產品等微型零件的理想選擇。
通過 EtherCAT 實時通信是關鍵
EtherCAT 可為復雜的運動結構提供實時通信。由于微型零件使用的塑料非常少,很難實現在不影響熔體質量的情況下保持加工溫度。MHS 采取的工藝是在塑料熔體到達閥口前才將其加熱到加工溫度,這樣可以延長材料塑化時間,大大減少浪費。
4 通道 EtherCAT 熱電偶輸入端子模塊 EL3314 和 TwinCAT Temperature Controller(TF4110)使得該實施成為可能。MHS 使用了 14 個公差要求為 ± 0.1 °C 的加熱器。EL3314 和溫度控制軟件的表現非常出色。倍福 AX5000 伺服驅動器中還配備了 AX5721 編碼器選項卡,支持高分辨率的線性編碼器。TwinSAFE I/O 和驅動器功能用于控制安全鎖、急停按鈕和安全轉矩關斷(STO)功能選項。
倍福的 AX5000 伺服驅動器驅動用于實現水平運動的 AL2815 直線伺服電機和用于實現垂直運動的 AL2412 直線伺服電機,以控制開模和合模運動。“如果沒有 EtherCAT 在 I/O 和驅動器中的實時功能,就不可能快速達到 10 μm 的精度。”MHS 的設計部經理 Ryan Craig 說道。
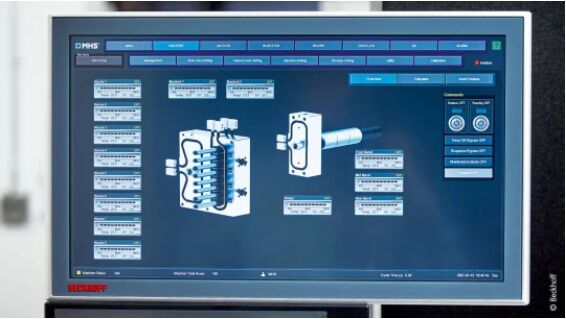
MHS 選擇了倍福的 21.5 英寸 CP3921 多點觸控控制面板,為操作人員提供了更大的透明度和可用性。
兼顧高產能與高品質
“倍福基于 PC 的自動化技術幫助我們實現了高動態線性運動軌跡精度,通過電子郵件發送日志以防止出現故障,連接云端并與第三方設備(如相機和烘料機)通信。”MHS 公司高級自動化工程師 Amir Abbas Shoraka 解釋道。
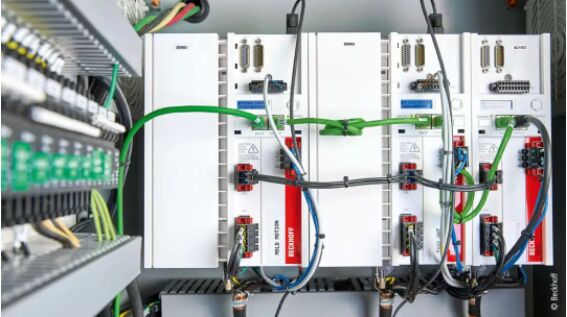
倍福的 AX5000 系列伺服驅動器用于高動態地控制螺桿、線性模具運動和側裝式機器人的運動。
緊接著,MHS 想要進一步提升產能,于是在 2020 年開始將 M3 從 8 x 1 個微型零件型腔模塊擴展到 8 x 4 個模塊,對于由此誕生的速度更快的 32 腔版本,它們能夠使用相同的控制架構。32 腔版本在側面還加裝了一個高速機器人,它以 0.4 毫秒移動 1000 毫米的速度進入單元,再以 0.4 毫秒的速度出來。AX5000 驅動器與兩臺 AM8042 伺服電機以及一個外部制動電阻用于實現上述過程。
在新的 Alpha M3-D32 中,62 個加熱器控制器在同一個控制平臺上工作,以 5 毫秒的周期時間控制軸和設備的動作時序。“除了機器人技術之外,M3 設備上還添加了一些控制智能,以及用于零件檢測和模具安全的視覺系統,它們都通過 EtherCAT 通信。我們使用性能同樣強大的基于 PC 的設備控制器實現了這一切,未造成任何性能損失。”Amir Abbas Shoraka 說道。MHS 在 EtherCAT 方面取得了巨大成功,因此公司也決定加入 EtherCAT 技術協會。
最早的 M3 設備就已經超越了行業標準,可在一個實際工作日內零浪費地平均生產 170,000 個微型零件。例如,如果零件的重量為 10 毫克,那么整個生產過程正好需要 1 公斤塑料顆粒。即使是聚醚醚酮(PEEK)及其它高熱材料,M3 也能達到相同的效率和品質。“從 2016 年的第一臺 M3 微注塑機起,零件的原型參數與大批量生產的加工參數就一直保持一致。”MHS 公司創始人 Harald Schmidt 說道。
M3-D08 縮小了微成型的質量差距,而 Alpha M3-D32 在不影響其在壓力、溫度和時間方面的可重復性的情況下具有更高的產能。M3 系列在設備運動、注射、冷卻、頂出和機器人方面可以達到 4 秒或更短的周期時間。擴大規模后的系統的平均日產量達到 69 萬個零件,是以前系統產量的四倍多。
|